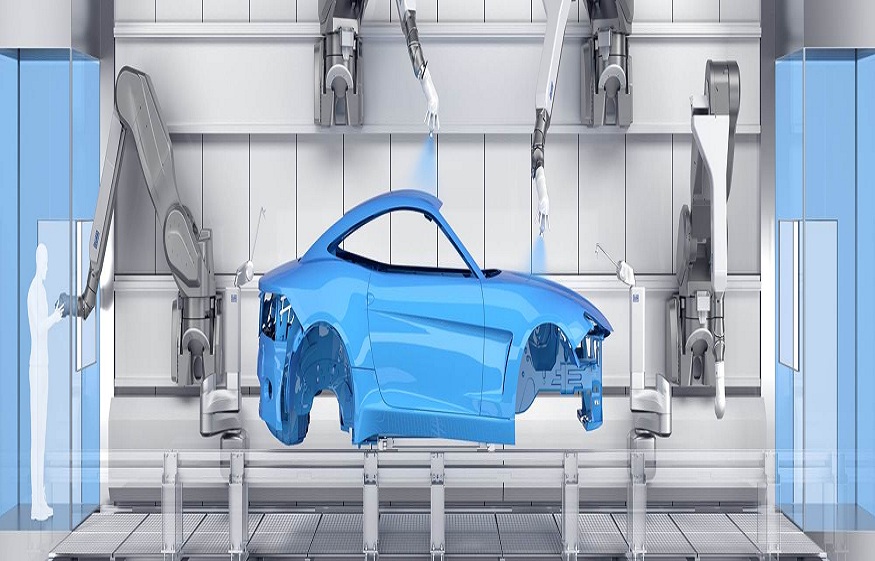
Can Upgrading Your Industrial Paint Booth Really Cut Production Costs?
industrial paint booths, the right improvements can actually trim expenses in ways most shops never expect. When every second and spray matters, a smarter setup starts paying off fast.
Maximizing Throughput with Optimized Booth Airflow Designs
Airflow inside a paint booth might seem like a behind-the-scenes detail, but it directly affects how fast and clean each job gets done. A well-designed industrial paint booth moves air evenly, pushing overspray out and bringing fresh air in without dead spots or turbulence. This keeps the work area clear and helps painters get smooth coverage in fewer passes. The result? Jobs finished faster and more consistently, which means more products moving out the door in less time.
An optimized airflow system also reduces the chance of rework. If air isn’t flowing correctly, paint may dry unevenly or dust may settle before the finish cures. That leads to do-overs, wasted time, and unhappy customers. When production speeds up without quality slipping, the entire operation runs smoother. So even though a better airflow setup may not look flashy, it’s one of the biggest hidden money-savers in any industrial paint booth.
Enhanced Energy Savings via Infrared Curing Integration
Heating a large paint booth takes a lot of energy, especially during the curing process. Traditional systems rely on warm air that takes time to heat up and circulate. But when an industrial paint booth adds infrared curing panels, that heat is delivered directly to the surface of the part. It’s faster and way more efficient because there’s less heat lost in the air.
Infrared curing can cut drying times nearly in half, which also reduces how long fans and heating systems run. That slashes power bills and speeds up the entire production line. With less heat escaping into the workspace, the building stays cooler, and ventilation systems don’t have to work as hard. This kind of upgrade turns a costly step in the process into a quick, energy-smart solution that keeps saving money every day it’s used.
Reducing Rework Costs through Superior Contaminant Control
Nothing slows down production like having to redo a paint job because dust, hair, or debris landed on a freshly coated surface. Inside a basic booth, even tiny airborne particles can ruin a finish. But when an upgraded industrial paint booth includes better filters and pressurized airflow, those particles stay out. Cleaner air means cleaner jobs.
Shops that install higher-grade filtration systems and tack-friendly interiors notice fewer paint defects and touch-ups. Every time a part is painted right the first time, it saves labor, materials, and energy. Plus, better contaminant control helps maintain a more professional, predictable workflow. No one enjoys surprise rework, and a booth that keeps the air pristine helps prevent those surprises before they happen.
Strategic Equipment Customization for Long-term Cost Efficiency
Not every shop needs the same booth. One-size-fits-all setups often include extras you don’t use or lack features you really need. Customizing an industrial paint booth to fit the job—whether it’s parts size, volume, or finish requirements—keeps energy and labor from being wasted. For example, a booth built specifically for tall machinery parts can use vertical airflow, reducing heating zones and air volume where it’s not needed.
Long-term cost savings come from smarter designs, not just smaller bills. Custom layouts make it easier to move parts in and out, reduce overspray clean-up, and optimize lighting where it matters most. The paint team works more comfortably and faster, and equipment wear stays low. Over time, every bit of that efficiency adds up, creating a booth that pays for itself through smooth daily operation.
Cutting Downtime by Transitioning to Dual-Use Spray-Cure Booths
In traditional setups, parts are sprayed in one area and cured in another. Moving them adds time, increases handling risks, and limits how many jobs can run at once. Upgrading to a dual-use spray-cure industrial paint booth changes the game. These systems allow spraying and curing to happen in the same space—no transfers, no wait time.
Switching between spray mode and cure mode is fast and easy, especially with automated controls. Downtime between jobs drops significantly, so production doesn’t have to pause just to change booths or move parts. Fewer moving parts also means less maintenance and repair. It’s one of those upgrades that seems small but makes a big difference where it counts—on the clock and in the budget.
Improved Material Yield through Precision Spray Environment
Every ounce of paint costs money, and not all of it ends up where it should. A poorly balanced booth lets too much paint drift or dry in the air. That waste adds up. A precision-controlled industrial paint booth, though, manages air pressure, temperature, and humidity so that paint sticks exactly where it’s aimed. That means better coverage with less product.
Painters also work faster when they can trust the booth’s conditions to stay steady. No more guessing if humidity is throwing off the spray or if a sudden draft will mess up the coat. Consistent performance leads to less overspray, fewer touch-ups, and longer intervals between cleanings. In the end, more of the paint goes on the product, and less of it goes down the drain—literally and financially.